Ongoing Energy Projects
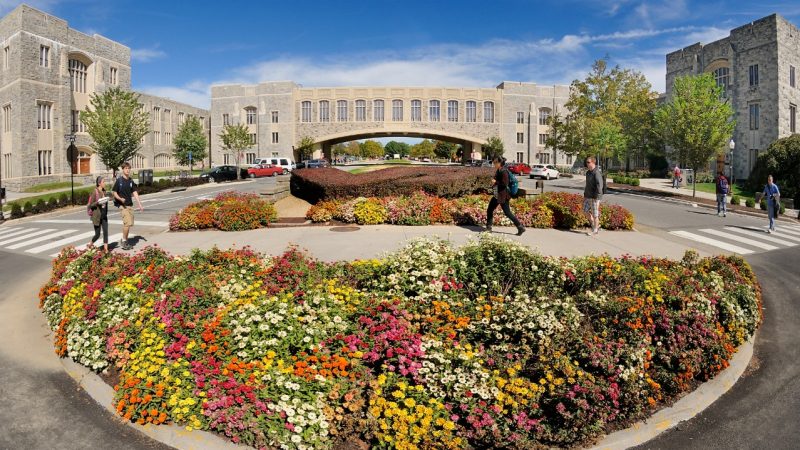
The Facilities Department is commited to helping the university reach its goal of improving energy efficiency where and whenever possible in campus buildings and has several programs in place to that end.
The following ongoing initiatives are year-round efforts:
Energy efficiency
The university strives to incorporate energy efficient products into new building construction as well as in the renovation of older buildings on campus. Using products that meet Energy Star® or EPA® standards significantly reduces water and electrical consumption while maintaining or even improving performance.
Demand Response
Since 2010, VT has participated in the Pennsylvania, Jersey, Maryland (PJM) Demand Response program which is designed to improve the reliability of the electric power grid. The program encourages electricity users to reduce their load during the times when there is a high stress on the power grid. This is common during the summer months when air conditioning and refrigeration are at their full use. The University agrees to voluntarily reduce its electric load in response to grid emergency situations which helps to protect the integrity of electric grid and earn revenues.
Winter and Summer Shutdowns
During the winter break as well as other holidays when students are not present and campus buildings are generally less occupied, the university conserves energy by shutting down appliances, heating and cooling systems in non-critical areas, and entire buildings that are not in use. Doing so results in considerable savings in utility bills, prolonged lives of the mechanical systems and reduced greenhouse gas emissions. Throughout the break, Facilities are continuously monitoring the temperature and humidity in the spaces and makes adjustments to the operation schedules based on weather conditions.
Laboratory Ventilation Energy Reduction Program
This program targets the optimizing of this system. Laboratory buildings are four to six times more expensive to operate compared to the administrative or classroom buildings and the lab ventilation system accounts for more than 50% of the overall energy consumption. Targeting these systems results in significant energy savings. Continuously measuring and verifying the ventilation rates in the labs helps Facilities comply with VT Health and Safety standards and reduce energy waste and greenhouse gas pollution. This leads to cleaner air at Virginia Tech as well as a noticeable reduction in energy consumption.
In some of the research buildings, a reoccurring problem arises when fume hoods are left open for extended periods of time, resulting in a loss of energy. In 2017, a green request for proposal (RFP) was submitted that outlined a plan for energy savings, specifically for fume hoods. This solution was to automate the fume hoods in buildings so that they would shut off when not being used to save energy since each fume hood uses roughly the same energy as 3.5 households per year. This project has an estimated cost of $3,500 per fume hood upgraded with an annual savings of $1,200 per hood with a total payback time of 2.9 years with foreseeable future savings for the university as well as significant greenhouse gas emissions. Furthermore, Environmental Health and Safety requirements state that fume hoods must not exceed 10 air changes per hour. The fume hoods are tested to ensure they meet these standards.
Currently, an automated fume hood sash has been installed in Kelly Hall. This device allows the sash to automatically shut, preventing the potential energy loss through a left open sash. Moving forward, more of these devices plan to be implemented around Virginia Tech’s campus.
Retro-Commissioning and Existing Building Commissioning
Retro commissioning and existing building commissioning is when old buildings that may or may not have been commissioned are revisited and the equipment is checked for performance. If the equipment does not perform up to standard, then it is reprogramed. As part of the reprogramming, the building’s automation system is fine-tuned, which includes the calibration of sensors, testing of control sequences, testing and balancing, programming updates, equipment scheduling, etc. Some of the buildings around campus vary greatly in age, Lane Hall being built in 1888 and the New Classroom Building in 2016, showing that there is a wide variety of needs for different buildings around campus to ensure they are all preforming at their highest standard.
Thermal Imaging of Campus Buildings
Thermal imaging is a technique used to generate images that help identify sources of energy loss. What is produced showed warm or cold spots around the building that display where heat or conditioned air is escaping. This is usually perform in the winter to find building envelope deficiencies such as holes and cracks in the envelope, leaking window and door seals and other areas of uncontrolled infiltration etc. The use of this technique helps Facilities improve building insulation to allow for continued energy savings.
Steam Trap Testing
A steam trap is a device used to trap and condense steam to not only save steam/water but also to save heat and energy. If these devices are faulty or have a leak, this could pose a problem to the surrounding area or result in a loss of energy and water. A steam trap test is conducted by examining the exterior of the steam trap to determine if there are any visual impairments, in addition to using a thermal camera to see if there is any thermal leakage. Steam trap testing should be performed regularly to ensure that no problems go unnoticed for an extended period of time.
Lighting Upgrade
Upgrades to lighting include a gradual switch to LED bulbs in buildings to save on electricity use in the long term. This is due to the energy efficiency and long lasting ability of LED lights. Lighting upgrades also include the transition from manual to automatic or motion detecting light switches to prevent lights from being left on. This is done by gradually replacing lights that have burned out with either a more efficient 25W tubular light or an LED tubular light.
Mechanical Insulation
Mechanical insulation is the insulation surrounding pipes, HVAC systems and other machinery that is used for heating or cooling. This insulation is often overlooked but very important, especially when water or air are heated or cooled and then subsequently moved over a distance. In addition, mechanical insulation can also be used to prevent the area around the pipe from being heated or cooled, which could interfere with the functions of nearby machines. When less of the desired temperature is lost, then less has to be produced to compensate, resulting in energy savings and reduced greenhouse gas emissions.
Building Automation Upgrade
Building automation involves a central system that controls mechanical heat and cooling in buildings. The system controls when heating and air conditioning turns on to maintain a comfortable temperature within the building. This is done through a Siemens automation system that can be upgraded as standards change.
For more information on any of these projects, contact the Office of Energy Management at 540-231-6348.